中壳残余应力检测和振动时效处理 试验报告
根据中国重汽集团 (以下称甲方)委托济南西格马科技有限公司(以下称乙方) 进行的中壳残余应力分析及振动时效处理的试验合同协议,济南西格马科技有限公司已于2011.12.13完成了合同协议规定的全部工作,现报告如下:
1、试验对象:甲方10挡粗加工毛坯,材质为HT200,弹性模量为126GPa,泊松比为0.26.
2、试验地点:乙方厂内。
3、试验时间:2011.12.7-2011.12.13。
4、残余应力检测方法:电测盲孔法。应变花采用BSF120-1.5CA-T。孔径1.5mm,孔深1.8mm。每个点打孔后经过3小时监测,以消除孔边塑性及蠕变的影响。乙方同时启用了3台ASMB2-32静态应变测试设备(见附录4)。
5、振动时效工艺:同时启用了4台乙方生产的SSEON100B科学振动时效设备(见附录5)、按国家标GB/T25713-2010进行时效工艺参数选择并利用曲线观测法快速判定振动时效的效果。中壳时效装卡方式采用2件并联方式,即每件彼此壳对壳、加工面朝两侧。每次时效2件。
6、试验过程:
6.1时效前对3件中壳毛坯进行残余应力检测
3个中壳均在A面向横隔面及边缘处共测了10点,K面向测了4点。
6.2 对包括6.1中已检测完残余应力的3件在内的共计23件中壳毛坯进行振动时效
每2台中壳并联在一起进行振动时效,按GB/T25713-2010进行时效工艺参数选择,过程见图4-1。
6.3时效后对前面测过残余应力的那3件中壳毛坯进行残余应力检测:
对经过时效的6.1中已检测完残余应力的3件中壳进行振动时效后的残余应力检测,确定振动时效后的残余应力值。继续利用6.1的编号。3个中壳的测点位置都相同并与时效前一样,仍见图1、图2。
3个壳体每个的A面向横隔面及边缘处共测了10点,K面向测了4点全部试验过程有甲方专门技术人员跟踪、监督。
7、 振动时效和残余应力检测的相关标准见附录1、附录2,ASMB2-32 的检定证书见附录3。
8、 分析:
9.1根据表4-1和4-3,中壳时效前残余应力分布规律如下:有8个点处等效残余应力数值较高,为最可能引发变形的部位。根据机加工的位置可知:机加工变形的主要因素为在其中3个点处的残余应力。
9.2根据原始时效曲线图5-1、5-2、5-3(壳3在上面)、5-4(壳1在上面,壳2在下面)、5-5、5-6、5-7、5-8、5-9、5-10、5-11、5-12,按GB/T25713-2010对它们利用曲线观测法快速判定振动时效效果,可见:所有工件均达到标准要求。
9.3根据表4-3和表4-4,对比时效过程导致的等效应力的变化,6个点处的残余应力降低较多。可知:引发中壳变形的主要部位变为该6个点。
9.4根据表4-2和4-4,可见,经时效后中壳残余应力分布规律如下:4个点处等效残余应力数值较高,为后续机加工最可能引发变形的部位。后续机加工变形的主要因素变为其中1个点处的残余应力。
9.5 根据表4-4,经过本次简单振动时效后,4个点处的等效残余应力数值较高,可知该中隔整体残余应力数值较高,所以,后续对该中隔的铣削及镗孔仍将引起中壳的较大变形。
9、 结论:
10.1 振动时效前,中壳中8个点位置处的残余应力数值较高,容易引起机加工或使用工况下的变形。若不做任何时效降应力处理,后续对中壳的机加工将导致中壳的较大变形。
10.2 振动时效可有效降低其中3个点处的残余应力,但对另5个点处效果不明显。
10.3两个销轴孔的间距在加工后的变形并不是因法兰面的加工所致,而是加工残余应力较高的中隔面所致。
11、建议:
11.1 建议甲方对更多批次的铸件进行铸造及热处理所致残余应力进行测试,掌握其分布规律,从而改善铸造及热处理工艺。还通过了解其残余应力分布规律,预测机加工可能改变何处的应力平衡、引起那些形位公差的改变,以优化机加工工艺。
11.2建议甲方通过对装卡引起的静态应力、机加工工装装卡产生的弹性变形进行测试,了解中壳在从工装上取下之后的装卡所致弹性恢复变形对2个定位销孔间距的影响,从而通过改善工装及装卡工艺提高定位销间距的精度。
11.3建议甲方通过测试机加工产生的新残余应力或残余应力的重新分布,了解中壳在从工装上取下之后机加工所致的弹性变形,从而预测或控制定位销间距的精度。
11.4若要通过振动时效降低其中3个残余应力幅值较大的点处的残余应力,需研制专门工装。
图1 3个壳体与2台ASMB2-32专用残余应力测试仪器 现场
图2 壳1 振前现场 应变花布置图
图3 壳2振前现场应变花布置图
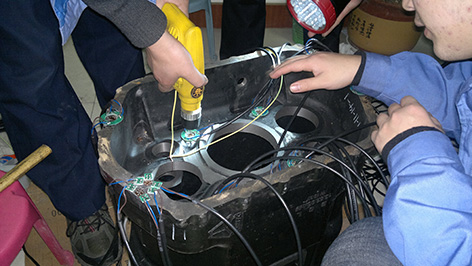
图4 壳体2-2点的残余应力测试曲线
图5 23台中壳壳体振动时效 现场局部1